[르포] 인텔 프로세서 조립 거점, 페낭 PGAT를 가다
[지디넷코리아]
[페낭(말레이시아)=권봉석 기자] 인텔은 21일(이하 현지시간) 진행된 '테크투어' 행사를 통해 반도체 다이 상품화를 위한 최종 과정을 수행하는 PGAT(페낭 조립·테스트 시설)를 각국 기자단에 공개했다.
PGAT는 인텔 페낭 캠퍼스 중 'PG8' 빌딩에 위치해 있고 반도체 최종 조립 과정을 수행하는 'PGAT 1', 완성된 반도체를 출하 전 마지막으로 테스트하는 'PGAT 2'로 구성되었다.
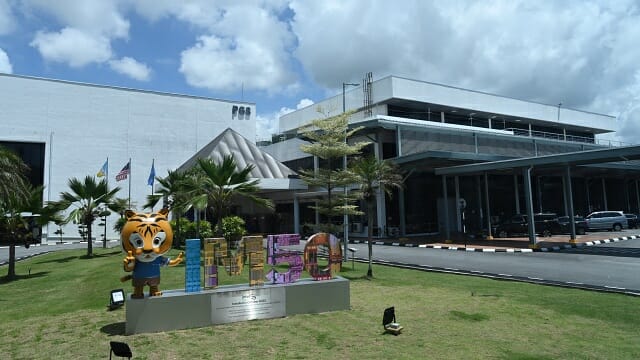
최근 수 년간 출시된 코어·제온 프로세서 뿐만 아니라 올 3분기부터 본격 출하될 코어 프로세서 '메테오레이크'(Meteor Lake)도 이 곳에서 최종 조립되어 각 PC 제조사에 출하된다.
■ 한결 가벼워진 방진 태세...정보보안은 강화
각국 기자단을 안내한 현지 인텔 관계자는 "PGAT 시설이 24시간 365일 운영되기 때문에 식당 역시 근무자들을 위해 24시간 운영된다"고 설명했다. 식당 입구에는 '할랄 인증을 받지 않은 식품은 반입할 수 없다'는 경고문이 붙어 있다.
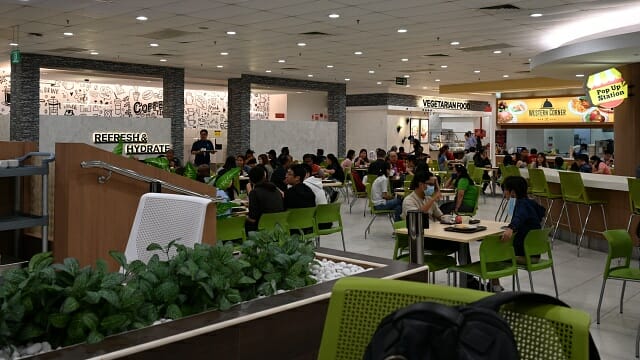
PGAT 내부 입장을 위해 덧신과 두건, 라텍스 장갑, 상하 일체형 방진복에 보안경까지 착용해야 하는 것은 지난 해 이스라엘 키르얏 갓(Kiryat Gat) 소재 반도체 생산시설 '팹28'(Fab 28) 방문시와 다름이 없다.
이미 웨이퍼 형태로 완성된 제품을 취급하는 만큼 각종 조치는 다소 완화되었다. 압축 공기를 온 몸에 뿜어 외부 먼지를 떨어내는 과정이 생략되었고 웨이퍼를 보호하기 위한 노란색 조명도 찾아볼 수 없다.
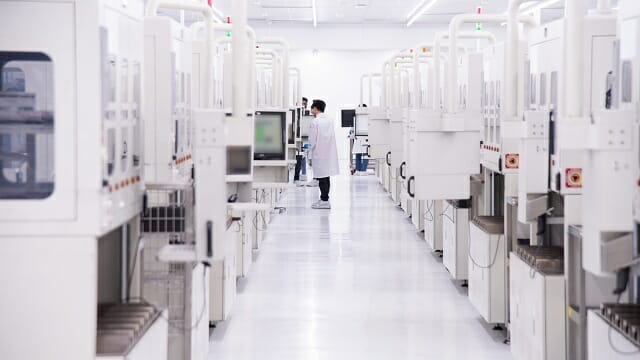
단 정보 통제는 지난 해보다 한층 더 엄격해졌다. 클린룸용 메모장과 펜을 지급했던 작년과 달리 올해는 어떤 것도 기록으로 남길 수 없다. 모든 생산 장비와 제품 시험용 기기에 탑재된 시판 메모리나 SSD 등도 아예 제조사를 알 수 없도록 철저히 가렸다.
■ 칩 부착·반도체 보호용 에폭시 주입
PGAT 1에서 진행되는 반도체 조립 첫 단계는 '칩 부착'이다. 테이프 릴에 감겨 공급된 반도체 다이를 공기로 빨아들인 다음 반도체 기판 위에 올린 다음 열과 압력을 가해 기판 위에 고정하는 '열압축 접합'(TCB) 과정을 거친다.
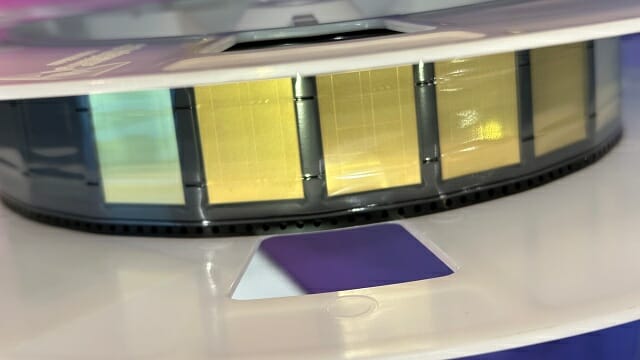
인텔 관계자는 "현재 가동중인 TCB 장비는 최대 5만 개 접점(Bump)을 6초 안에 이어붙일 수 있는 성능을 지녔다"고 설명했다.
칩 부착 단계를 거친 반도체는 그 상태 그대로도 작동하는 데 아무런 문제가 없다. 그러나 다이가 외부 열이나 습기, 충격 등으로 손상되는 것을 막고 보다 단단하게 고정할 필요가 있다.
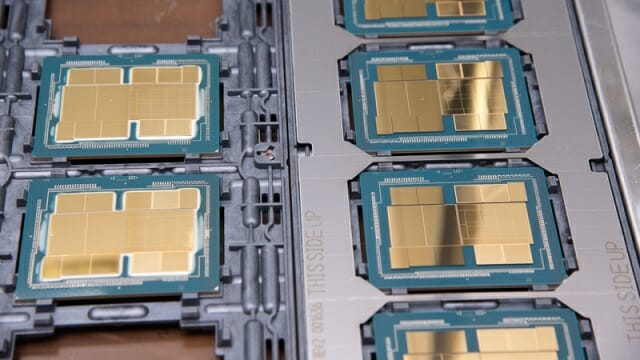
이를 위해 플라스틱 소재인 에폭시(Epoxy)를 녹여 반도체 다이와 기판 사이에 주입해 강도 등을 보강한다.
■ 열 배출 돕고 반도체 다이 보호하는 히트 스프레더
4세대 제온 스케일러블 프로세서(사파이어래피즈)나 데이터센터 GPU 맥스(폰테베키오) 등 제품은 300W를 넘는 전력을 소비하는 동시에 상당한 열을 방출한다.
다이 위에 직접 방열판과 냉각팬을 설치할 경우 무게나 고정장치 압력으로 다이가 깨질 수 있다. 이 때문에 다이를 덮어 보호하는 동시에 열을 분산시킬 수 있는 금속 뚜껑인 '히트 스프레더'를 올리는 과정을 거친다.
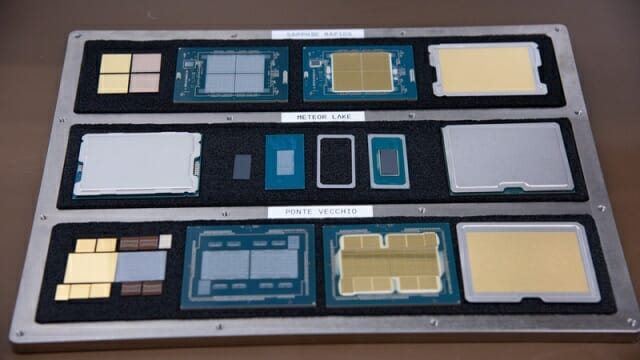
히트 스프레더 안쪽 중 반도체 다이가 직접 닿는 부분에는 금도금을 통해 전도율을 높이기 위한 작업도 함께 진행된다. 메테오레이크 등 모바일(노트북) 프로세서는 각 노트북 제조사가 자체 설계한 방열판 등을 장착하기 때문에 PCB 기판이 뒤틀리는 것을 막는 얇은 금속판인 스티프너를 다이 주변에 두른다.
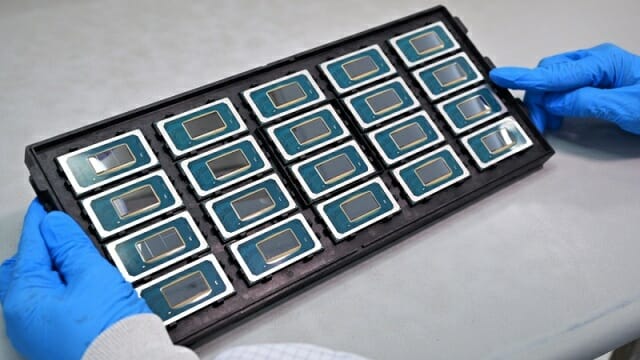
히트 스프레더 장착이 끝난 반도체 표면에는 레이저로 제품 모델명과 로트(Lot) 번호 등 정보를 새긴다. 이 과정을 마치면 조립 과정은 모두 마무리된다.
■ 출하 전 고온·고전압 검사...실제 환경 검증까지 확인
PGAT 1에서 히트 스프레더까지 부착을 마친 반도체는 통로 하나를 사이에 두고 연결된 테스트 시설인 PGAT 2로 옮겨진다. 통로 중간까지 일행을 안내한 인텔 관계자는 "이제 방진복 두건을 벗어도 좋다"고 말했다. 머리카락 등이 불량을 일으킬 위험을 벗어났다는 의미다.
PGAT 2는 PGAT 1에서 완성된 제품에 불량이 있는지 검사하는 과정을 수행한다. 트레이에 담긴채로 운반된 제품은 이미지 센서를 통해 앞뒤를 자동으로 촬영한 다음 레이저 마킹 불량, 접점 불량 등을 솎아내는 1차 검사 단계를 거친다.
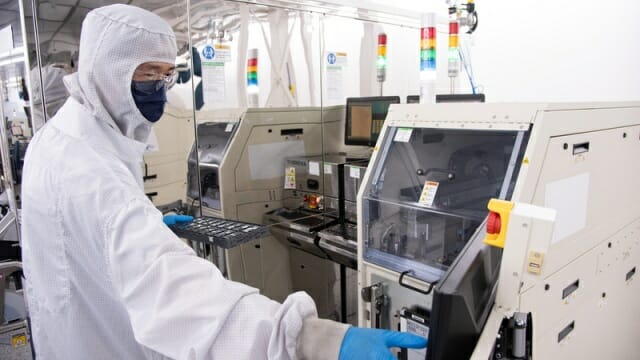
그 다음 고온과 고압에서 버티는 지 감시하는 '번인 테스트'를 거친다. 이 과정을 거치지 못한 제품은 품질 관리 부서로 되돌아가 원인 분석 대상이 된다.
최종 단계는 각종 프로세서가 실제로 투입될 고객사의 PC 제품이나 서버 제품과 같은 환경에서 윈도·리눅스 등 각종 운영체제를 설치해 문제없이 작동하는 지 확인하는 PPV(프로세서 플랫폼 검증)이다. 이 과정까지 통과한 제품은 전세계 각지로 공급된다.
■ "향후 차세대 패키징 기술까지 페낭서 직접 소화"
현재 PGAT는 2020년대 이후 인텔이 추진하는 차세대 패키징 기술인 EMIB, 포베로스 등을 직접 처리할 수 없다.
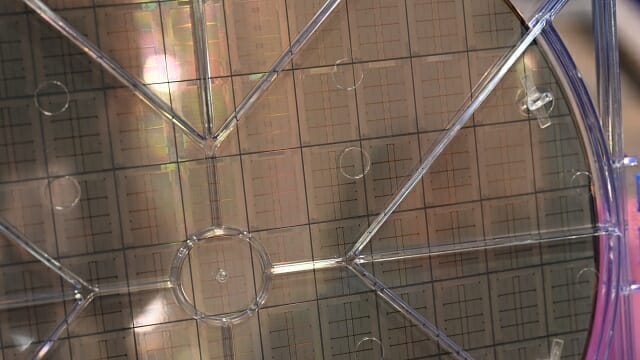
이들 반도체 생산을 위해서는 미국은 물론 대만 TSMC 등이 생산한 반도체 다이를 일단 미국 오레곤 주 소재 생산시설 등에 한 데 모아 합친 다음 다시 말레이시아로 보내야 한다.
문제는 이런 과정을 거치면서 물류 비용은 물론 운송 시간 등에서 그만큼 손해를 본다는 것이다. 인텔은 이런 문제를 해결하기 위해 2021년부터 페낭과 쿨림 등지에 첨단 패키징 기술을 소화할 수 있는 '펠리컨', '팰콘' 등의 시설을 추가 건설하고 있다.
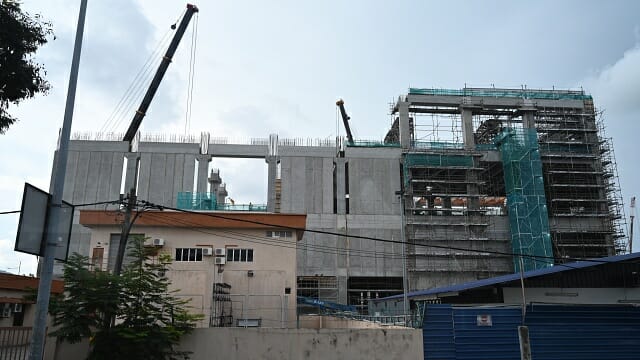
두 시설은 2024년 완공 예정이다. 인텔 관계자는 "두 시설이 완공되어 가동에 들어가면 전통적인 패키징은 물론 EMIB, 포베로스 등 향후 인텔 첨단 공정 역시 말레이시아에서 수행할 수 있게 된다"고 설명했다.